【www.zhuodaoren.com--热点事件】
可逆轧机流体控制系统水泵工艺设备(一)
乳化液控制系统在冷轧可逆轧机上的应用
乳化液控制系统在冷轧可逆轧机上的应用
摘要:本文从乳化液的功能描述、用途、系统应用等方面详细阐述了乳化液在莱钢1500mm冷轧单机架可逆轧机中的应用。并介绍了乳化液控制系统的配置和基本功能。
关键词:冷轧;可逆轧机;乳化液;控制
1、引 言
冷轧通常是用热轧后得到厚度为2-4mm、经过酸洗处理的钢圈作坯料,用六辊可逆轧机轧成厚度在1.5mm-0.2mm的薄板。被轧制的钢材对轧辊表面有相对的滑动,在很高的轧制压力和轧制速度下,这种相对滑动转化成巨大的摩擦热。在无良好的冷却润滑的情况下,这两种有害的热能将引起轧辊和带钢的温度迅速上升,使轧辊辊形变化、强度和表面硬度降低。不仅不能保证轧材的质量,而且有损坏轧辊,断带的可能。
轧机乳化液系统是轧机众多流体系统中的一个,是唯一一个承担工艺润滑任务的系统。莱钢1500mm可逆冷轧机乳化液冷却系统主要由地上乳液站,地下乳液站和喷射阀组三部分组成。
2、乳化液用途
轧机乳化液系统主要用于达到以下目的:
①润滑辊逢,减少摩擦系数,从而降低轧制压力,降低能耗和减少轧辊损耗;
②在轧后带钢表面形成一层油膜,在短期内起到防止带钢生锈的目的;
③润滑轧辊,可在轧制变形区形成一层油膜,将轧辊与带钢在轧制变形区处于干摩擦状态转化为半干摩擦状态,从而减少轧辊间摩擦;且在极压状态下油膜能保存完好;
④冷却轧辊和带钢,带走轧制过程转化的变形热,防止缠辊和辊裂以减少轧辊的损坏,从而提高板形控制精度和减少轧辊磨损;【可逆轧机流体控制系统水泵工艺设备】
⑤可带走附着在带钢和轧辊表面的部分杂物,具有一定程度的清洁作用,并减少轧制中所产生的金属粉尘。
3、系统功能描述
轧机使用后的乳化液自回流到乳化液回流箱内,由地下泵组打至地上经磁链式过滤器后除去颗粒含铁杂质,用循环泵送至真空纸带过滤器处理。经处理后
可逆轧机流体控制系统水泵工艺设备(二)
轧机厚度自动控制系统设计

龙源期刊网 .cn
轧机厚度自动控制系统设计
作者:卜闪闪
来源:《建筑工程技术与设计》2015年第10期
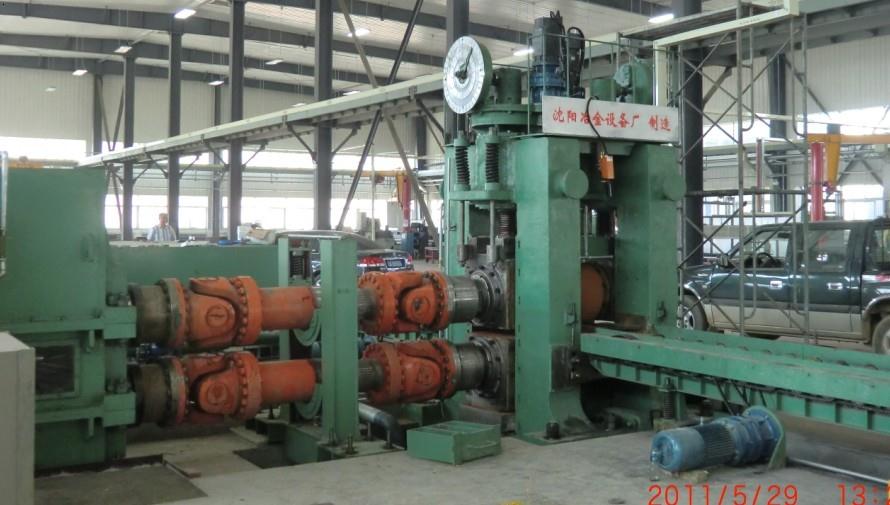
摘要:随着社会经济的发展,对板带产品的质量和精度要求越来越高。厚度精度就是板带产品的重要质量指标之一。本文针对轧机AGC技术的现状,以及轧机厚差产生的原因进行了分析。在此基础上,对轧机AGC进行分析,以APC为主要研究对象,选用PLC作为系统的控制器,将位移传感器测得的位移量经A/D转换送给PLC来控制步进电机,从而控制阀,通过轧制力来改变辊缝厚度实现轧机厚度控制。
关键词 :轧机 AGC APC
1 引言
轧机又称轧钢机,轧钢机就是在旋转的轧辊之间对钢件进行轧制的机械,轧钢机一般包括主要设备(主机)和辅助设备(辅机)两大部分。轧钢机按轧辊的数目分为二辊,三辊式,四辊式和多辊式,轧钢机通常简称为轧机。
板带厚度精度是板带材的两大质量指标之一,板带厚度控制是板带轧制领域里的两大关键技术之一。带钢纵向厚度不均是影响产品质量的一大障碍,因此,轧机的一项重要课题就是带钢厚度的自动控制。厚度自动控制系统是通过测厚仪或传感器对带材实际轧出厚度连续进行测量,并根据实测值与给定值比较后的偏差信号,借助于控制回路或计算机的功能程序,改变压下装置、张力或轧制速度,把带材出口厚度控制在允许的偏差范围内。实现厚度自动控制的系统称为“AGC"。
我国近年来从发达国家引进的一些大型的现代化的板带轧机,其关键技术是高精度的板带厚度控制和板形控制。板带厚度精度关系到金属的节约、构件的重量以及强度等使用性能,为了获得高精度的产品厚度,AGC系统必须具有高精度的压下调节系统及控制系统的支持。 而对于轧机来说产生厚差的原因大致可分为三大类:
(1)轧机方面的原因:轧辊热膨胀和磨损、轧辊弯曲、轧辊偏心和支撑辊轴承油膜厚度等都会产生厚度波动。它们都是在液压阀位置不变的情况下,使实际辊缝发生变化,从而导致轧出的带钢厚度产生波动。
(2)轧件方面的原因:厚度偏差会直接受到坯料尺寸变化的影响。它包括来料宽度不均和来料厚度不均的影响。
(3)轧制工艺方面的原因: 轧制时前后张力的变化、轧制速度的变化等。
可逆轧机流体控制系统水泵工艺设备(三)
轧钢机控制系统
【可逆轧机流体控制系统水泵工艺设备】
成绩:
课 程 设 计 报 告 书
所属课程名称 机电传动控制(含PLC) 题 目 分 院 机电学院 专 业、班 级 机械设计制造及其自动化 学 号 学 生 姓 名 指 导 教 师【可逆轧机流体控制系统水泵工艺设备】
目 录
前言
1 课程设计任务书„„„„„„„„„„„„1 2 总体设计„„„„„„„„„„„„„„„2
2.1控制系统框架„„„„„„„„„„„„„2 2.2主线路接线图„„„„„„„„„„„„„2
3 硬件系统设计„„„„„„„„„„„„„2
3.1系统所需的硬件„„„„„„„„„„„„2 3.2系统设计„„„„„„„„„„„„„„„3 3.3 I/O端口接线 „„„„„„„„„„„„„4 3.4 I/O地址分配 „„„„„„„„„„„„„4
4 程序设计„„„„„„„„„„„„„„„5
4.1总体设计过程,程序流程图„„„„„„„„5 4.2操作过程„„„„„„„„„„„„„„„6 4.3 PLC梯形图操控程序 „„„„„„„„„„7 4.4语句表 „„„„„„„„„„„„„„„10 4.5实验现象图块„„„„„„„„„„„„„10
5 程序调试及结果分析„„„„„„„„„„13 6 总结„„„„„„„„„„„„„„„„„13 7 参考文献„„„„„„„„„„„„„„„14
前言
轧机的主要设备有工作机座和传动装置;工作机座由轧辊、轧辊轴承、机架、轨座、轧辊调整装置、上轧辊平衡装置和换辊装置等组成。轧辊是使金属塑性变形的部件,它包括轧辊轴承、轧机机架、轧机轨座、轧辊调整装置、上轧辊平衡装置等。
中国于 1871 年在福州船政局所属拉铁厂 ( 轧钢厂 ) 开始用轧钢机轧制厚 15mm 以下的铁板, 6 ~ 120mm 的方﹑圆钢。 1890 年汉冶萍公司汉阳铁厂装有蒸汽机拖动的横列双机架 2450mm 二辊中板轧机和蒸汽机拖动的三机架横列二辊式轨梁轧机以及 350/300mm 小型轧机。随着冶金工业的发展,现已有多种类型轧机。
现代轧机发展的趋向是连续化、自动化、专业化,产品质量高,消耗低。 60 年代以来轧机在设计、研究和制造方面取得了很大的进展,使带材冷热轧机、厚板轧机、高速线材轧机、 H 型材轧机和连轧管机组等性能更加完善,并出现了轧制速度高达每秒钟 115m的线材轧机、全连续式带材冷轧机、 5500mm宽厚板轧机和连续式 H 型钢轧机等一系列先进设备。
应用PLC控制达到自动化。PLC即可编程序控制器,英文全称Programmable Controller,简称PLC。它是一个以微处理器为核心的数字运算操作电子系统装置,转为在工业现场应用而设计,采用可编程序的存储器,用以在其内部存储执行逻辑运算、顺序控制、定时/计数和算术运算等操作指令,并通过数字式或模拟式的输入/输出接口,控制各种类型的机械或生产过程。PLC的程序编制,不需要专门的计算机编程语言知识,而是采用了一套以继电器梯形图为基础的简单指令形式,使用户程序编制形象、直观、方便易学,调试和简易的用户程序编制工作,就灵活方便地将PLC应用于生产实践之中。
随着生产力和科学技术的不断发展,人们的日常生活和生产活动大量的使用自动化控制,不仅节约了人力资源,而且很大程度的提高了生产效率,又进一步的促进了生产力快速发展,并不断的丰富着人们的生活。

【摘要】早期的自动控制系统是依靠继电-接触器来实现的,其特点是:结构简单、价格低廉、抗干扰能力强,可以实现集中控制和远距离控制,但是其采用固定接线,通用性和灵活性差;又采用触点的开关动作,工作频率低,触点易损坏,可靠性差。
自从1969年美国DEC公司研制出世界上第一台可编程逻辑控制器(Programmable Logic Controller:PLC)以来,经过三十多年的发展与实践,其功能和性能已经有了很大提高,从当初用于逻辑控制和顺序控制领域扩展到运动控制和过程控制领域。可编程逻辑控制器(PLC)也改称为可编程控制器(Programmable Controller:PC),由于个人计算机也简称PC,为了避免混淆,可编程控制器任然被称为PLC。
本设计是基于PLC的轧钢机控制系统,利用传感器S1来检测传送带上有无钢板,若S1有信号(即开关为ON),表示有钢板,电机M3正转,信号指示灯MZ亮。S1的信号消失(即为OFF),检测传送带上钢板到位的传感器S2有信号(为ON),表示钢板到位,电磁阀动作,指示信号灯YU1亮,电机M3反转,指示信号灯MF亮。此时,Y给一向下压下量,S2信号消失,S1有信号,电机M3正转„„如此重复上述过程。
【关键词】PLC 传感器 电磁阀 钢板 正反转
辽东学院课程设计报告书 机电传动控制
辽东学院
1 课 程 设 计 任 务 书
课程设计题目: 轧钢机控制系统 课程设计时间:自 2011 年 7 月 11 日起至 2011 年 7 月 21 日。 课程设计要求:
当启动按钮SD按下,电机M1、M2运行,传送钢板,检测传送带上有无钢板的传感器S1的信号(即开关为ON),表示有钢板,电机M3正转(MZ灯亮);S1的信号消失(为OFF),检测传送带上钢板到位后的传感器S2有信号(为ON),表示钢板到位,电磁阀动作(YU1灯亮),电机M3反转(MF灯亮)。Q0.1给一向下压下量,S2信号消失,S1有信号,电机M3正转„„重复上述过程。
Q0.1第一次接通,发光管A亮,表示有一向下压下量,第二次接通时,A、B亮,表示有两个向下压下量,第三次接通时,A、B、C亮,表示有三个向下压下量,若此时S2有信号,则停机,须重新启动。
学生签名:
2011年 7月 11日
课程设计评阅意见
评阅教师: 2011年 月 日
可逆轧机流体控制系统水泵工艺设备(四)
西门子技术在棒材轧机改造中的应用
摘要:江苏苏钢集团有限公司810棒材轧机在改造过程中采用了西门子的交直流传动装置、PLC技术、现场工业总线和工业组态软件等,使改造后的轧机系统满足了适用性、可靠性,提高了操作、维护的方便性,提高了系统的响应速度和控制的精度,从而达到了本次改造的目的。 关键词:棒材 轧机 西门子技术 改造
0 引言
江苏苏钢集团有限公司棒材厂810棒材轧机,系引进于1980年在英国Brymbo钢厂建成投产的的二手设备,苏钢于2006年恢复建设该生产线,并以此为契机,对现有生产线存在的问题进行适当改造,以达到顺利生产出优质产品的目的。
该轧制线主要?准810mm二辊可逆式粗轧机、?准810mm二辊可逆式中轧机、?准670mm二辊不可逆精轧机、轧后设有两条锯切线、两套翻转式冷床、钢坯收集台架等组成。
由于整个轧制区和热锯区设备的原传动装置和控制系统系上世纪七十年代末的技术和产品,存在着控制精度差、无备件、维护困难等一系列问题,因而有必要在此次恢复过程中对其升级改造。本次改造通过选型对比选用了西门子的交直流传动装置、PLC技术、Profibus现场工业总线技术和WinCC工业组态软件等,本文对其应用情况作简单的介绍。
1 传动技术
1.1 辅助直流电机调速装置 轧制区的辊道、机械手、压下装置,以及热锯区的定尺挡板、冷床、冷床输入链等都由直流电机驱动,选用SIMOREG 6RA70系列全数字控制整流装置,其具有结构紧凑,方便组柜节省占地面积。装置本身带有参数设定单元,不需要其他的任何附加设备即可完成参数的设定,所有的控制、调节、监视及附加功能都由微处理器来实现,具有自适应最佳传动控制功能,达到最优化的方式运行。具有强大的保护功能:过流、断流、过压、欠压、超速、缺相、断电、失磁、测速机断线、堵转、电机过热等等,以及综合的自保护功能。标准的Profibus接口,传输速率快,可通过Profibus-DP传到PLC系统,并将有关电机运行参数,如电流、速度、温度数据、变化趋势曲线及报警信号集成到主控室MMI画面,实现在MMI画面集中操作、监视和启动。
1.2 粗、中轧机直流主传动 粗、中轧主传动采用直流电机驱动,其功率分别高达3000kW和2000kW,分别由容量为4800kVA、3200kVA的三绕组整流变压器供电。两套传动装置的配置和控制原理基本相同,都由整流变两副边绕组分别经由两台6RA70控制的大功率SCR可逆整流桥整流后并联给电机电枢供电,满足大容量电机功率要求和过载能力。两台主控6RA70配置SIMLINK网,主从工作,完成装置间的电流平衡。同时6RA70通过配置的Profibus-DP接口,与轧线主控PLC系统联网交换数据。
1.3 变频调速装置 轧线上交流调速辊道电机控制系统采用集中整流单元+公共直流母线+逆变器+制动电阻的方案,逆变器选用西门子公司具有矢量控制功能的6SE70系列,采用公共直流母线结构,并实现网络控制。这种方式具有较高的性能价格比,在保证性能的前提下,可有效地节省投资费用,而且在运行过程中由于逆变器可将再生电能送回直流母线,可达到节能的效果,降低运行费用。装置还提供了完备的监控保护与故障自诊断功能,通过Profibus-DP接口与上一级自动化系统相连接,进行集中操作控制,监控,参数的设定和各种信息的交换。
2 基础自动化控制系统
基础自动化由轧制区1#主PLC(S7-400)、热锯区2#主PLC(S7-400)组成,二套PLC通过Ethernet连接,达到资源共享,快速交换数据的控制目的。主PLC中配置Profibus-DP现场通讯网络接口,其中主PLC通过1#Profibus-DP网与各操作台、箱、站内的ET200M相连,通过网络收集或发出各种反馈、操作及执行信息。另有2#Profibus-DP网与传动系统中各传动装置配备的CBP通讯板连接所有传动数控装置,用以控制各区相关的电气传动设备,实现快速传递数据的目的。
1#主PLC(轧制区)共配有5个ET-200远程站,分别放于粗轧机前操作室、粗轧机后操作室、精轧机操作室、1#油站和2#油站内,用于连接相应区域的各种信号。
1#主PLC控制内容主要有:粗、中、精轧机组入口\出口辊道的启停及速度控制;粗、中轧机组入口\出口的翻钢机、移钢机的动作控制;粗、中轧机组间T1、T2移钢机的控制;精轧主电机控制;粗、中、精轧机组辊缝的控制;轧制区域的液压站、润滑站、干油站、风机和水泵等的控制等等。
2#主PLC(热锯区)共配有10个ET-200远程站,分别放于冷床区操作室、1#线锯区操作室、2#线锯区操作室、T3/T4/T5操作室、E5主电室、锯区液压站、下料区液压站、T7T8液压站等,用于连接相应区域的各种信号。
2#主PLC控制的主要内容:两条锯切线辊道的启停及速度控制;热锯电机的控制;锯区和冷床区液压站、润滑站、干油站的控制;冷床输入、输出、连接辊道的控制;T3、T4、T5台架输入辊道的控制等等。
3 过程自动化系统
过程自动化系统的上位机由五台HMI(人机接口操作站)、一台工程师站组成,其中HMI1~HMI5分别放置于:粗轧机前操作室、中轧机前操作室、精轧机操作室、热锯操作室和冷床操作室。
HMI、工程师站系统均配以西门子WinCC 6.0工业组态软件,该软件功能强大,性能可靠,这一运行于Microsoft Windows 2000或XP下的Windows控制中心,已发展成为业界遵循的标准,开放的系统内核集成了所有SCADA系统功能。棒材厂轧线的人机接口(HMI)系统通过以太网相互之间连接,并与基础自动化系统连接,具备友好的图形化界面。主要功能包括:参数设定、设备控制、状态显示、事故报警、故障诊断、趋势分析六大类。基本的参数设定有:各轧机速度、定尺长度、轧辊直径、延伸率、原料成品规格、抛钢速度、压下量、各种限幅报警值设定等。
4 通讯网络
4.1 现场级-Profibus 基础自动化系统与各传动系统之间的设定值、指令和数据均通过PLC机架装配的Profibus-DP网络接口进行传送,提高了系统响应速度。
在现场I/O比较集中的地方均设有ET200M远程站,通过Profibus-DP网络化分布式控制,能够有效地减少项目的投资和现场施工量,增加系统的可靠性,方便现场的维护,系统结构灵活先进,符合控制系统发展趋势的特征。
4.2 系统网络级-Ethernet 以太网作为连接操作员站、工程师站和自动化系统站的系统总线,实现基础自动化系统与过程自动化系统之间及基础自动化系统各PLC之间的数据通讯,以太网在物理层上采用高防护等级的通讯线缆及光纤传输,提高了通讯的安全可靠同时保证了高速的通讯速率。在主控室、操作台站点集中的地点设网络交换机组成交换式快速以太网络,提高网络效率与网络带宽,同时方便移动式网络设备和二级(生产)管理系统的接入。
5 结束语
由于本次改造充分运用了西门子的交直流传动装置、PLC技术、现场工业总线和工业组态软件等技术,使改造后满足了轧机系统的适用性、可靠性,提高了操作、维护的方便性,提高了系统的响应速度和控制的精度。自改造后投运至今,实践证明,该系统达到并超越了原设计功能,安全可靠,能确保设备连续、可靠运行,满足高效、有序地组织生产的要求,从而达到了本次改造的目的。
参考文献:
[1]SIEMENS,SIMOREG DC Master使用说明书[M].天津:西门子电气传动有限公司,第6版2000年.
[2]SIEMENS,MICROMASTER 440通用型变频器使用大全[M].北京:西门子(中国)有限公司,第12/03版2000年.
[3]廖常初.S7-300/400 PLC应用技术[M].北京:机械工业出版社,第2版2006.
作者简介:徐利君(1965-),男,江苏苏州人,江苏苏钢集团有限公司棒材厂,工程师,主要从事电气自动化技术。
可逆轧机流体控制系统水泵工艺设备(五)
油气润滑的工作原理及其在莱钢型钢厂天车上的应用
【摘 要】简要介绍了油气润滑的工作原理及其在莱钢型钢厂天车上应用油气润滑技术上的情况。 【关键词】油气润滑;原理;天车;应用
0.前言
油气润滑是新型的“气液两相流体”技术的典型工业应用。油气润滑因具有润滑效果好、耗油量低、可精确计量给油、可实现高度自动控制和可使用润滑油品黏度范围大等优点,在自动化程度高的工业领域得到了广泛应用,尤其是在高温、高速、重载和使用环境恶劣的冶金领域,如冶金领域的辊道运输线、单机架和串列机架冷轧机、线材轧机的高速转动导位装置以及天车轮缘等。
1.油气润滑的工作机理
“气液两相流体”的形成和本质。
按照润滑介质存在的状态不同,传统的润滑方式可分为固体、液体和气体三类。“气液两相流体”润滑是一种介于液体润滑和气体润滑间的过渡润滑方式,具有液体和气体润滑的优点,避免了各自的不足,同时派生出液体和气体单独润滑方式不具备的优点。在一个管状的空间内。
2.技术参数及工作原理
2.1润滑对象
行车四个大车轮的轮缘及轨道
2.2天车参数
(1)主电机:110KW,AC380V。
(2)钢丝绳:17.5mm×2根。
(3)大车运转电机:22KW,AC380V。
(4)小车运转电机:11KW,AC380V。
(5)主减速机 ZQ640×2台。
(6)大车减速机 ZQ440×2台。
(7)直流电缆卷筒:JT220-20-6,AC380/220V。
(8)大车轮:?800mm×4个。
(9)小车轮:?500mm×4个。
(10)行车跨度:28.5m。
(11)电磁盘自重:4T×4台。
(12)总吊重:16T。
2.3油气润滑系统主要技术参数
(1)系统油压工作压力:60~100bar。
(2)系统气压工作压力:3~5bar。
(3)系统工作电源: 220VAC,50Hz。
(4)泵每行程输出油量:0.25ml/行程。
(5)泵工作的间隔时间:0~999sec之间调节。
(6)系统工作方式:PLC控制,间歇工作。
(7)系统电耗:约0.5KW/小时。
(8)润滑油消耗量:1L/500KM。
(9)润滑介质:GRALUBWFL000。
2.4工作原理
(1)基本原理:油气润滑技术是德国REBS公司的创新,它采用压缩空气连续作用带动油沿管道内壁不断地流动并形成涡流状地油气混合物(油和气并不真正融合也不会雾化),以精细油滴地方式导入轮缘上。压缩空气和油间歇供给,间歇时间和供油量可根据各润滑点的消耗量进行调节。油气润滑是利用压缩空气对润滑剂进行输送及分配的集中润滑系统。
油气润滑系统主要由供气部分、供油部分、油气混合器部分、电控部分和管路末端的喷嘴。SP-P10型气动泵装配在油箱里面靠近底部的位置,这种独到设计的目的是为了满足泵的压力和行程要求从而使泵吸油充分,同时也使得润滑剂能够充分、均匀地混合,采用含有固体颗粒的润滑剂时,这样做显得尤为重要。泵的排量为0.25毫升/行程。泵的回程复位借助于弹簧的作用,一旦驱动泵的压缩空气停止供应,弹簧就将柱塞回到初始位置。驱动泵的压缩空气由一个2位2通电磁阀进行控制,压缩空气最低为3bar,泵受驱动后就会供送初润滑剂。电磁阀关闭时,压缩空气供应停止,泵运行其吸入行程。润滑剂从泵供送出来后进入OLM油气混合块,在此和压缩空气混合后形成油气混合物并沿着管壁、TURBOLUB油气分配器等输送到喷嘴。油气由TURBOLUB油气分配器进行分配,TURBOLUB油气分配器的专利技术及特殊加工工艺可以确保油气按某一特定比例(如50%:50%或是其它比例)分配到润滑点。
电控系统:Rematic SGF2000SP型控制组件是一个电路板,它可以以距离控制的方式(也可以切换为时间控制方式)对天车轨道润滑系统的运行方式进行控制。当天车行驶了一定距离后(通过接近开关感应),2位2通电磁阀打开,压缩空气在驱动泵的同时供送到油气混合块、中间管路及喷嘴,随后泵准确地运行一个行程并将定量润滑剂供送至管路中并最终由喷嘴喷出,喷射持续的时间设定为6-8妙,一个喷射周期结束后,系统暂停工作直至天车运行的距离达到设定值时再开始另一个喷射周期,如此循环往复。系统对于天车运行距离的工作方式是可控的,在天车停止运行不用时,系统会停止工作以避免无谓喷射;而天车运行距离达到某个适当值时,系统即会被唤醒并开始工作。
(2)系统特点:由于天车上的压缩空气容量有限,因此喷射并不是连续不断的,而是每隔一段时间喷射一次-当然,每次喷射过程都是连续的并持续6-10秒的时间。在系统中,泵和喷嘴之间的中间管道大约含有10%的润滑剂和90%的压缩空气,这样的比例使压缩空气在喷射过程中能够对润滑剂产生作用并使之形成精细油膜,越靠近喷嘴油膜的厚度越小同时也越精细,喷到轮缘上的油膜层的厚度小于0.001mm,其宽度为10-15mm,10-30平方毫米的润滑剂量在数妙内以最精细的颗粒喷在轮缘上-在喷射过程中,车轮可以转很多圈;同时,由于压缩空气的作用,在管道中输送的添加有高比例耐压固体颗粒的润滑剂加速从喷嘴喷出并以150-200m/s的高速度喷到轮缘上,喷射过程干净利落并且确保天车在高速行驶的状态下喷射出的润滑剂也能突破车轮周围的空气流和行车风而精细地覆盖在机车轮缘上。整个喷射过程中都有润滑剂,喷射的时间越长,从喷嘴喷出的润滑剂越精细。但不管喷射时间越长,喷出的润滑剂量都是相等的,因为定量泵决定了润滑剂的供送量。
当天车行驶速度达到每小时5-10公里是,在车轮的轮缘周边会产生离心力,在润滑膜增厚和行驶速度加快的情况下,离心力会使得润滑剂得粘附力降低,因此喷射出来的润滑剂颗粒不能太大是非常重要的,试验表明当颗粒直径大于0.4mm,即体积大于0.03平方毫米时,离心力会使润滑剂飞溅。REBS的轮缘润滑系统由于喷射速度高,持续时间长,润滑剂并不会飞溅开来,不仅润滑剂的消耗小,同时又避免了润滑剂对天车和轨道沿线的污染。
3.天车油气润滑系统的优点
(1)系统采用REBS专有技术,润滑油在管道内形成超薄、精细的油膜,喷射出的油膜颗粒只有几十微米,准确的喷射在钢轨的侧面上,不会污染钢轨的表面或随车轮运转四处飞溅。
(2)系统采用含有固体颗粒(如石墨、铝粉)的润滑油,油膜有极高的耐压性能。
(3)系统由PLC控制,并由检测元件检测天车的运动,间歇喷射,以保证润滑油量不至过多而污染环境。
(4)系统的耗油量极低,约1L/500KM。
(5)系统的润滑效率极高,可大幅度提高天车轮缘的使用寿命,极大地降低了天车的运行和维护费用。
4.结论
莱钢中型型钢厂天车油气润滑系统按照现场实际情况进行改造、设定和调试,系统运行正常。按照实际统计数据,改造后的油气润滑系统比过去干摩擦状态时,延长了车轮的使用寿命3倍多,大大地减少了停机时间,除按照周期向主站添加润滑油外,系统处于无故障运行状态,成为一个名副其实不污染环境、高度机电一体化和低运行成本地免维护系统,完全达到了利用新技术改造落后润滑方式地目的。随着油气润滑技术进一步发展和其应用范围地进一步扩大,润滑设备和润滑状况将得到更好地完善。
本文来源:http://www.zhuodaoren.com/shenghuo341605/
推荐访问:可逆式轧机 可逆轧机招聘